Early blacksmith bellows
Have you ever wished you had a pair of bellows for your forge? Maybe you plan to cast some bronze, melt some glass or try out blacksmithing?
It's not as hard as you might think. Follow these easy instructions and you are good to go. Please take your time to read it all through first so you feel you grasp the whole concept and take everything into consideration before starting.
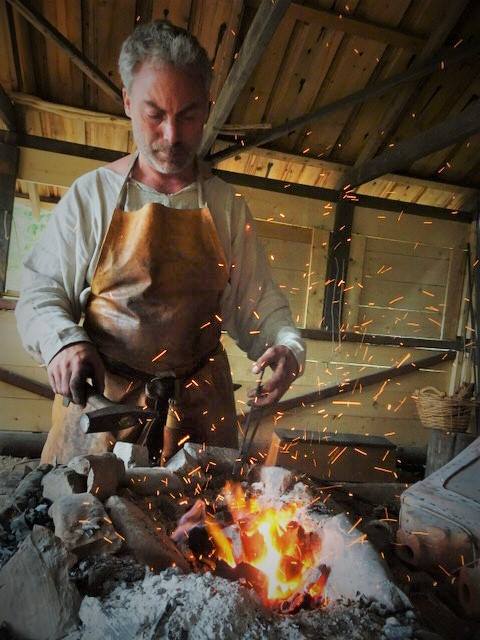
The first blacksmith bellows depiction I know of is from the Sigurdsristning in Sweden.

Image is link to original RAÄ web site.
As an aspiring blacksmith, after a few weeks of blacksmithing I wanted to make my own bellows. I took a range of photos along the way, and years later this article was formed from numerous requests for information on bellows.
Bellows are generally worked in pairs for evenly distributed airflow. Some depictions of single bellows are actually a later medieval two-chamber system where one bellow is used to fill another bellow for even air-flow distribution.
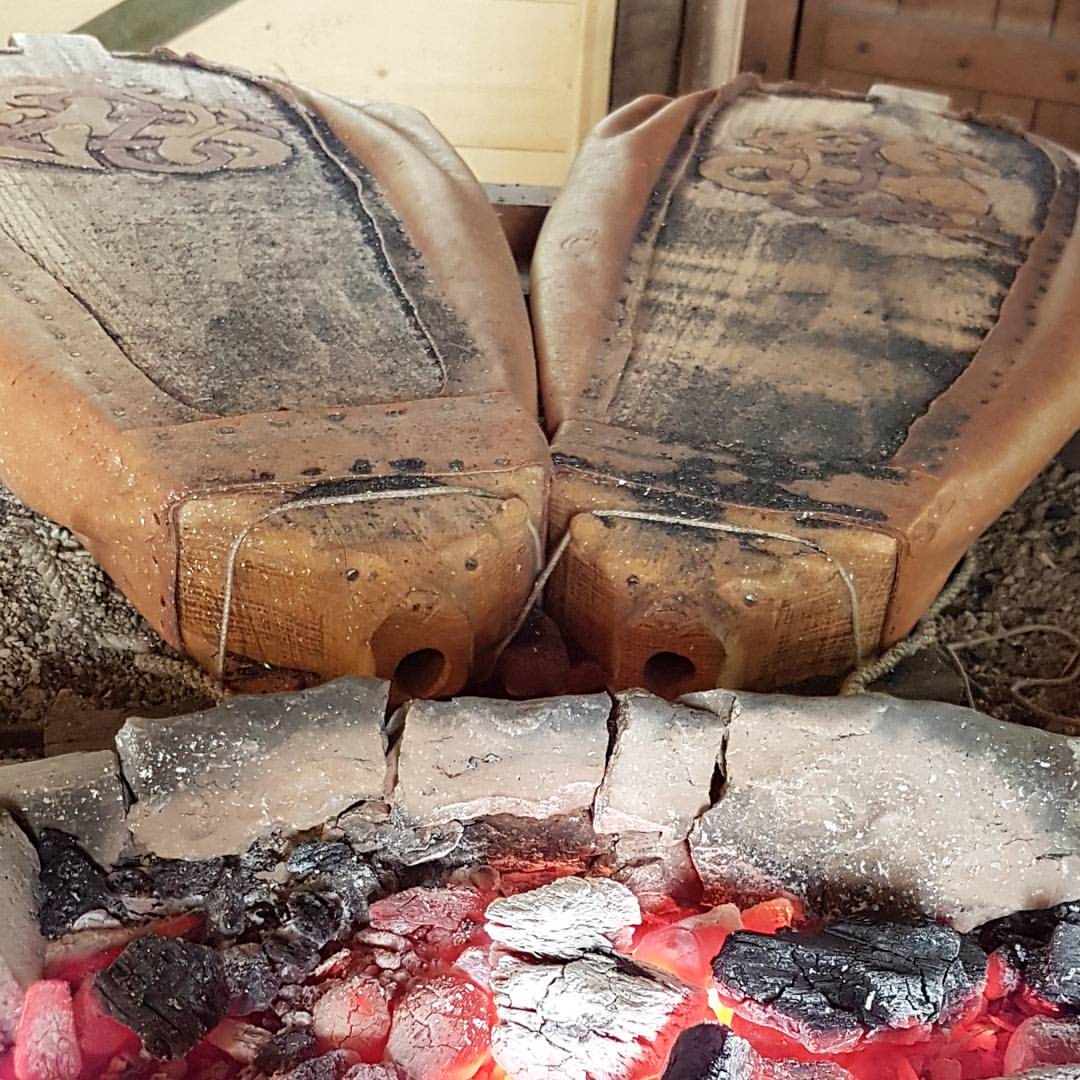
I should also quickly state that my work was based on an article on the Hantverkslagret.org website, but that article has since been pulled in some site update.
Along the way I also received great advices from a friend by the name of Robin Davies, with far more bellow making experience than me.
Building the bellows
The materials
Bellows are often made from wood and leather. Any board material will do for the bellow up-side and bottom, and any fabric like material will work for sides as long as it is tight enough to not too easily let air slip through. However, the less stretchy material the better.
You will need:
- Two pieces of wood like board material for the bellow bottoms, something like 120x45 cm each
- Two pieces of wood like board material for the bellow tops, something like 100x45 cm each
- Two blocks of wood about 15x20x5 cm for the nozzles
- Two pieces of leather like material for the bellow sides, something like 200x45 cm each and not too thin (could be sewn together from several pieces)
- A few smaller pieces of leather for hinges and vents
- Short nails with big heads for fastening the leather (could also be attached to the wood by sewing)
- A drill for making the holes
- Knives, saw, axe - woodworking tools for shaping the bellow top and bottom
- A light-weight hammer for fastening the nails when attaching the leather
The process
Shaping the bellow bottoms
The bellow bottoms will extend almost the length of the bellows, so it's best to start with these.
Bellow shape and size
The bigger the bellows the more airflow will you get, or the less manual lift frequency will be required since the airflow is also dependent on nozzle width. Making the bellows to small will eventually leave you annoyed. Most of the time bigger is better as long as your forge can fit them.
Most bellows are drop-shaped. This makes sense. You want to collect a lot of air inside them in the end where they are raised the most and push it out in a bellow body that is slowly getting narrower to increase the airspeed.
The nozzle blocks are fastened to the bottom of the bellows for the hinges to work while directing the airflow in a constant direction. For this to work the bottom pieces need to be longer than the top ones.
You don't need to figure out the front part exactly just yet, but it's good to be happy with the general form of them.
Personally, I used a good piece of ash wood I had laying around in my workshop. It was a bit old and twisted, so I had to plane them a bit and thin them out a bit. They were also from a part of the tree that made them un-even that I had to work with.
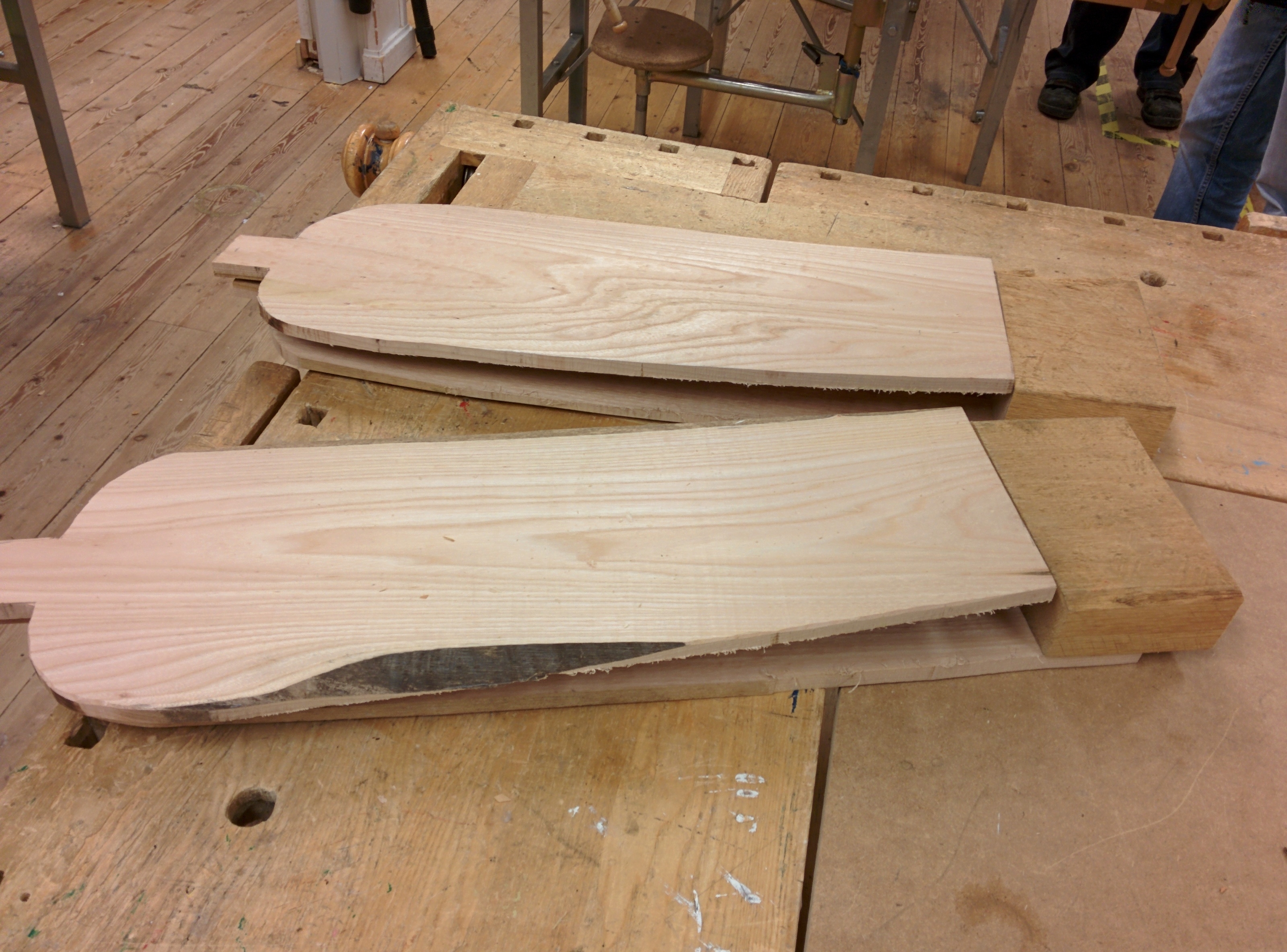
I've been asked if it's good to have thin pieces of wood in the bellow top and bottom. Thicker makes them heavier to carry around. The thicker the bottom the heavier they will be and the less they'll challenge your fastening system. Most people use the same material for top and bottom. The heavier the top material is the faster they close and the more air is pushed out of them per second, but you will also have to increase the lift frequency.
Fastening in the forge
Remember to think about how to fasten the bellow bottoms to the forge already when making them. Some forges are raised above the ground while
some forges are set on the ground so you'll have to pin the bellow bottoms to the ground to secure them.
You probably want a versatile fastening system that could be used for several different crafts and different forges.
Fastening is most important in the back end of the bellows since that's the end being constantly janked when lifting. However, the front part might move too and that's the end directing the airflow. The front-end fastening should be easily removed to be able to lift the bellow fronts away from the forge heat when taking breaks or when burning coal fall under them.
Eventually I opted for kind of a pin extruding backwards from the bellows and drilled a hole in them for fastening purposes by tent pins or rope for the backend and a rope-based fastening in the front end.
Vents
Most bellows I've seen have their vents in the bottom piece. This makes sense since the vent flaps will have gravity working for them and it's less risk of un-wanted stuff getting into the bellows. As my friend Robin said; -"You can hardly have to large vents.". The bigger the vents the easier the lifting of the bellows will become.
Vent backdraft locks are often in sturdy leather, fastened on the inside. Remember at what end of the vent you fasten the locks since storing the bellows is best with hanging locks.
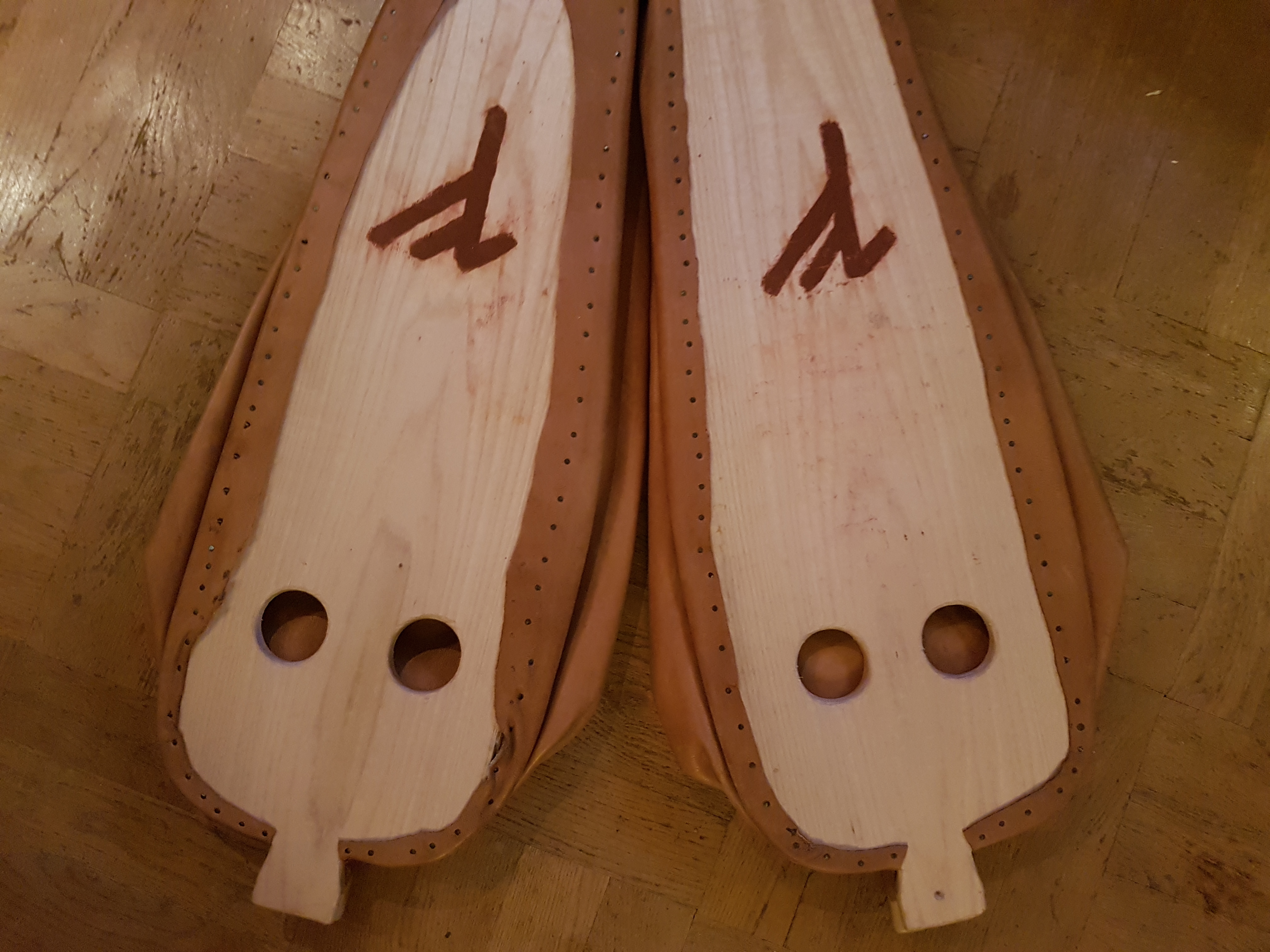
It could be better making numerous vents rather than one big vent if you do not trust your vent backdraft blocking material to not flex too much.
Key takeaways about bottom
- Prepare for large vents
- Remember the bellow bottom fastening system
- Store the bellows with free-hanging airlocks
Bellow lids
Place the board material upon the bottoms and draw a line following the shape of the bottoms. Remember that the left and right bellow bottoms might differ slightly so don't cheat by using the same one twice.
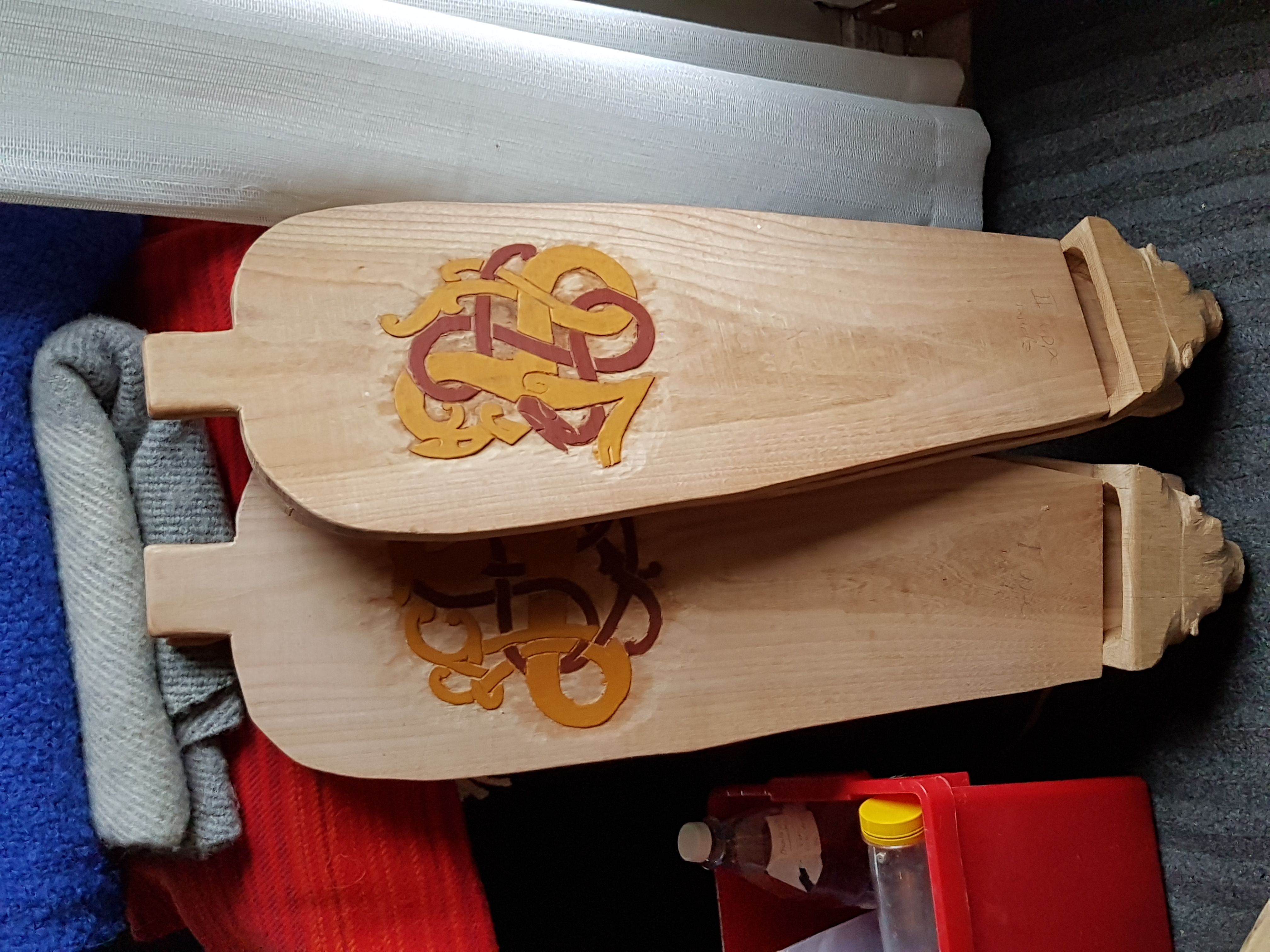
Remember as mentioned in an earlier section that the bellow bottoms should be longer than the top pieces due to leaving room for the nozzle blocks.
Lifting handles
Leave a handle centred in the back of the top piece if you don't have any other plan for lifting handle. I've seen bellows with handles attached to them on the top part, so there are definitely variant approaches.
As can be seen in the pictures I choose a similar tap as in the bottom bellow. That choice also was sprung out of an idea that it would be easier to pack the bellows if the shape was as regular as possible.
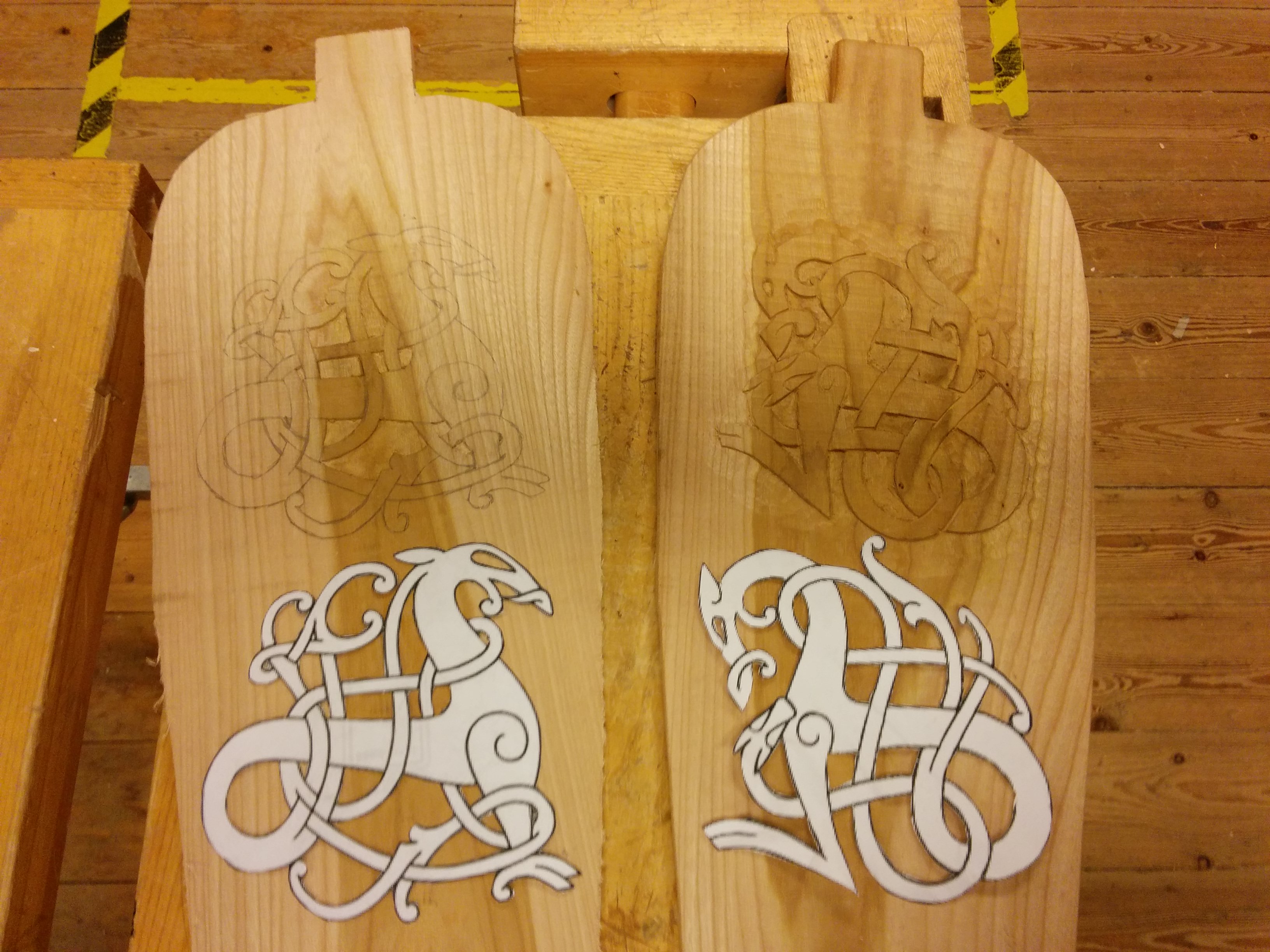
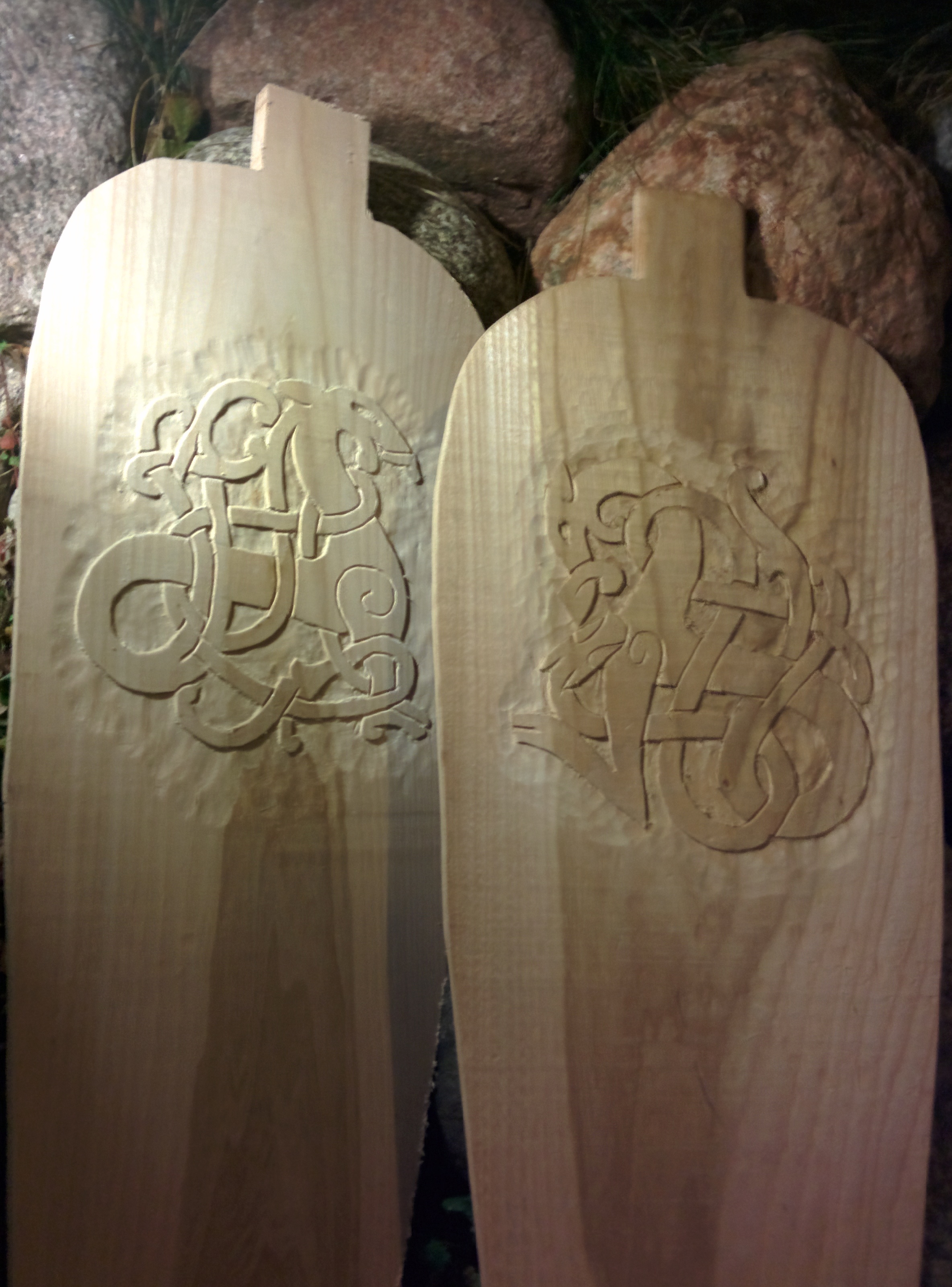
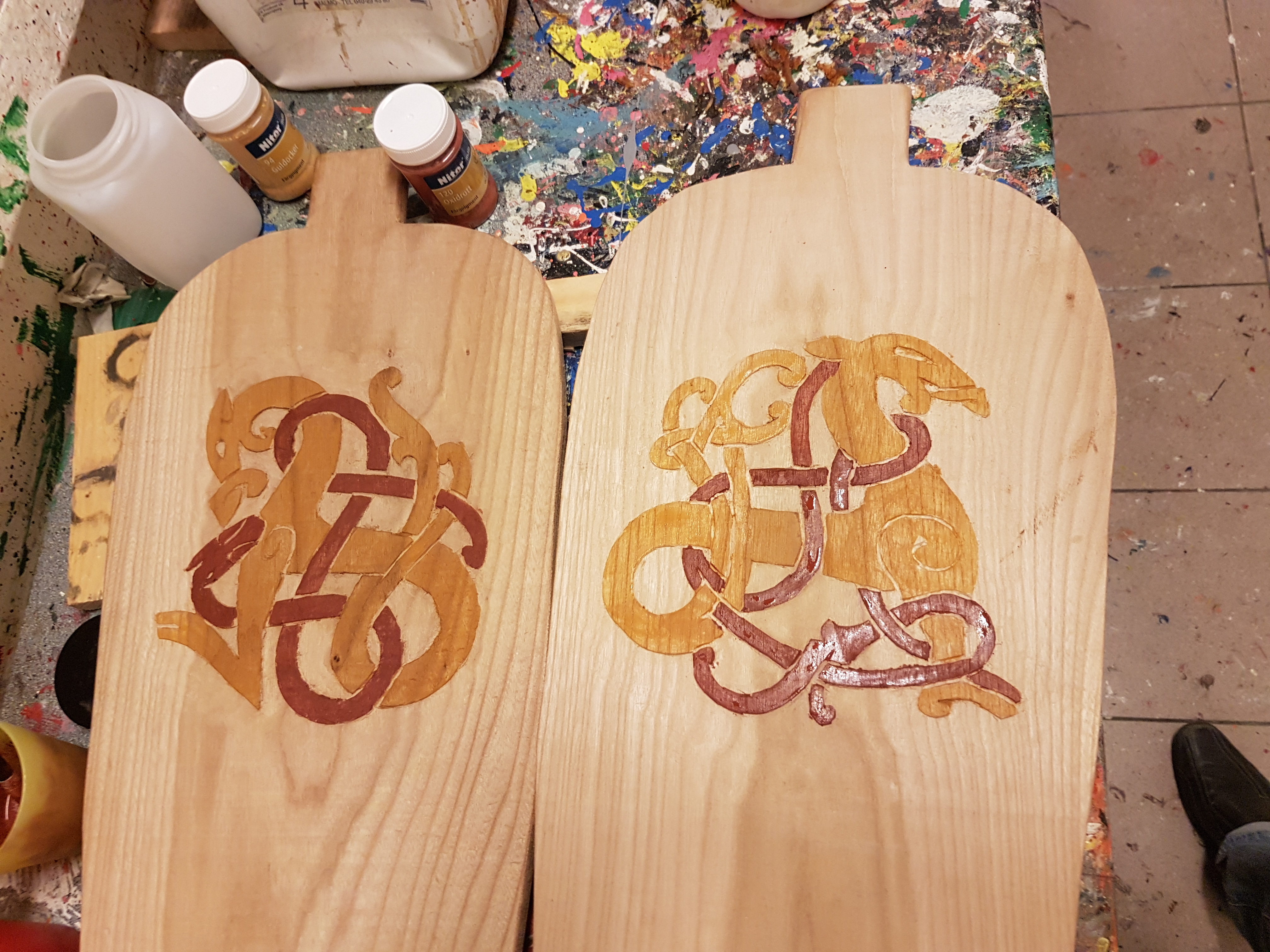
I've seen bellows with forged hinges attaching the top piece to the nozzle block. This is something I wouldn't recommend. They tend to squeak and after a few hours of constant squeaking it's terribly annoying. The leather material still needs to cover the hinge part so any metal hinges would need to be attached on top of the leather. If you choose to use metal hinges, remember to leave thickness enough for fastening in the front end of the bellow tops - or prepare to reinforce them on the underside of the bellow top piece.
Key takeaways about bellow top
- Lifting device
- Hinge types
Nozzles
The nozzles could be the trickiest part of the bellows. The goal is to avoid all sharp edges. Sharp edges make an obstacle for the airflow, building internal pressure rather than making the air exiting as smoothly as possible.
Enough material should be kept to hammer the nails down to fasten the leather while at the same time the nozzles should be wedged enough to allow alignment of the airstream.
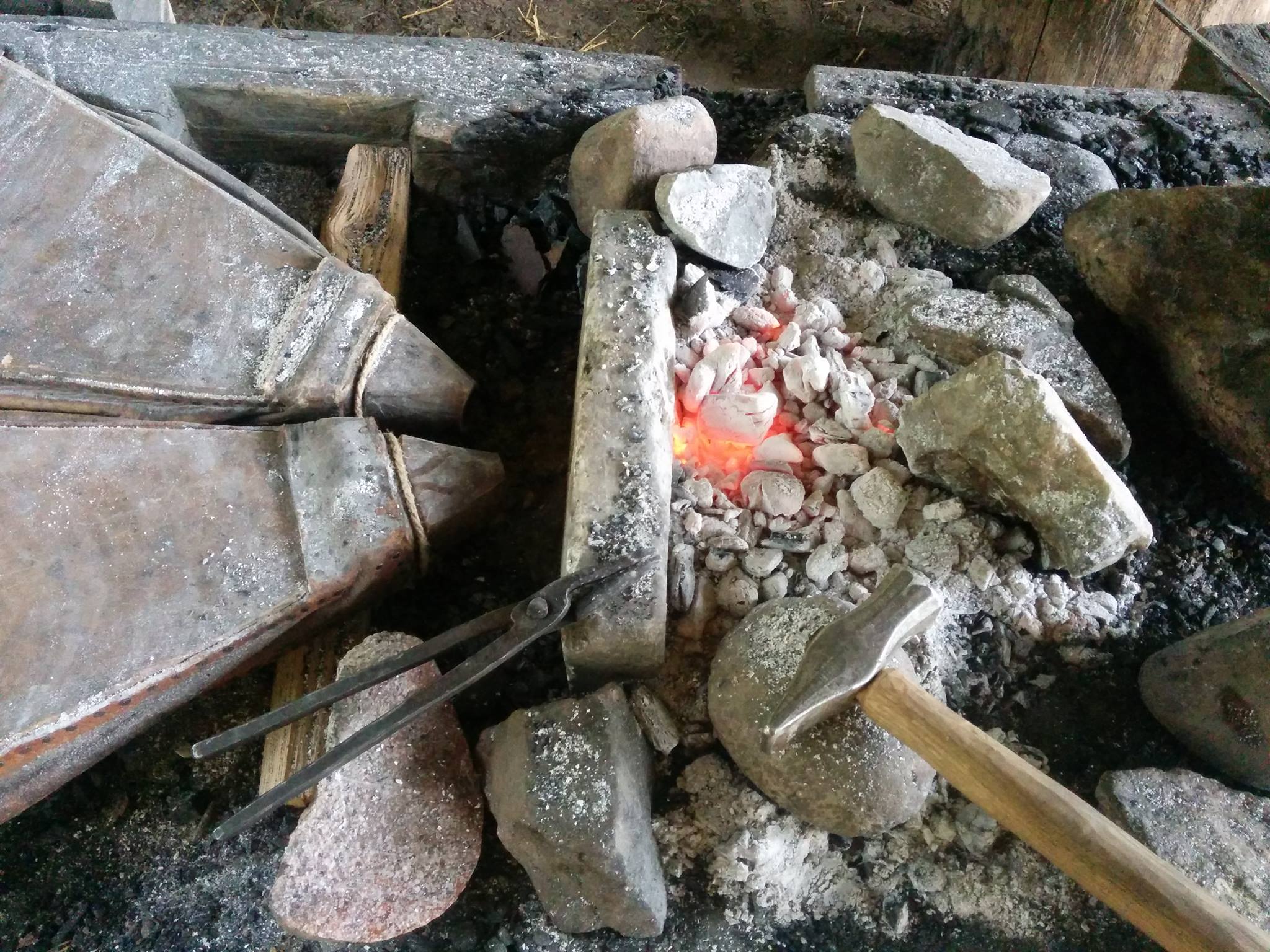
If nozzles are not fastened tightly they will drift away over time.
I received the advice to "think like if you are designing a football stadium that needs to be able to evacuate quickly". I'm not sure it's the very best of metaphors, but I got the general concept.
I've tried working with bellows with a nozzle block with only a drilled hole in them, and it's much harder work so you will want to spend some extra time cutting these to shape.

In the picture above here the nozzle block is turned upside-down. The open part of this shape is glued to the bottom piece of the bellow (so the side that is up in the picture goes down to the bottom piece). As can be seen the airflow should accelerate fairly un-obstructed out through the exit part of the nozzle.
The outside of the nozzle blocks doesn't matter that much. It's easier to store them if excess material is cut away. Personally, I made an attempt to decorate mine. It was meant to be bears, but the camp kids soon started calling them pig-bears which stuck since it actually was very fitting.
I love my trusty pig-bears.
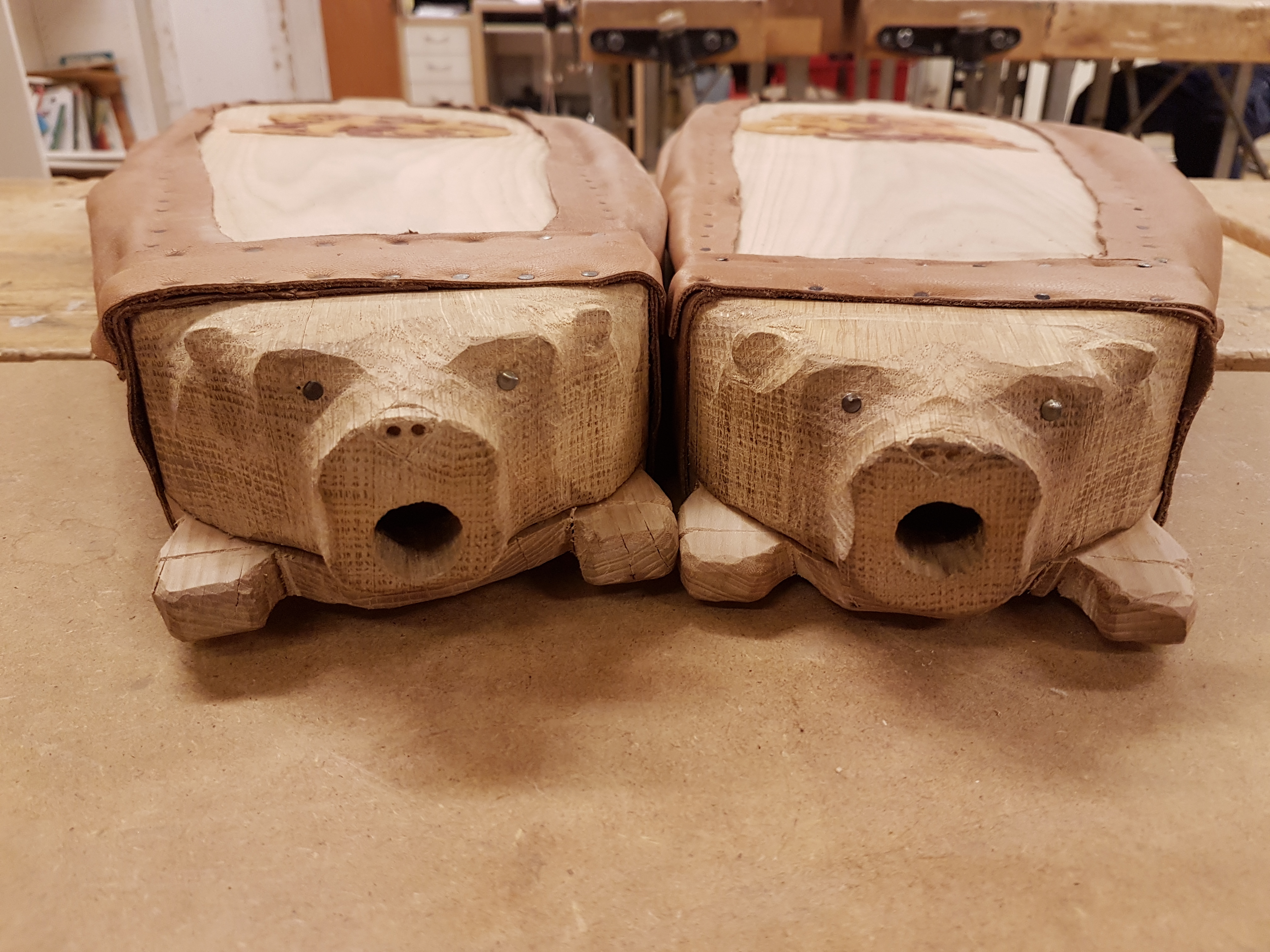
where the ears are meant to hold the string fastening them to the forge.
Another thing with the nozzle is keeping the very last few centimetres closest to the exit as a straight drilled hole to align the airflow for laminar flow to more easily direct the airflow towards the blaster stone.
Key takeaways about nozzle blocks
- Shape for smooth air exit
- Shape for bellow placement next to each other
- Keep last few centimetres of the exit hole totally straight to align airflow
Leatherworks
Sides
Remember to fasten the vent backdraft locks before attaching the sides.
The leather material should be sturdy enough to not be stretching due to difference in air preassure on the inside and the outside of the bellows. That would reduce the efficiency of the bellows. I've seen bellows where the leather has grown larger over time from use and leather being too thin. That makes for horrible bellows. In the last section of this article a mitigation example can be seen.
Prepare the leather as much as possible in advance. It will be trickier doing leather maintenance one the bellows are assembled.
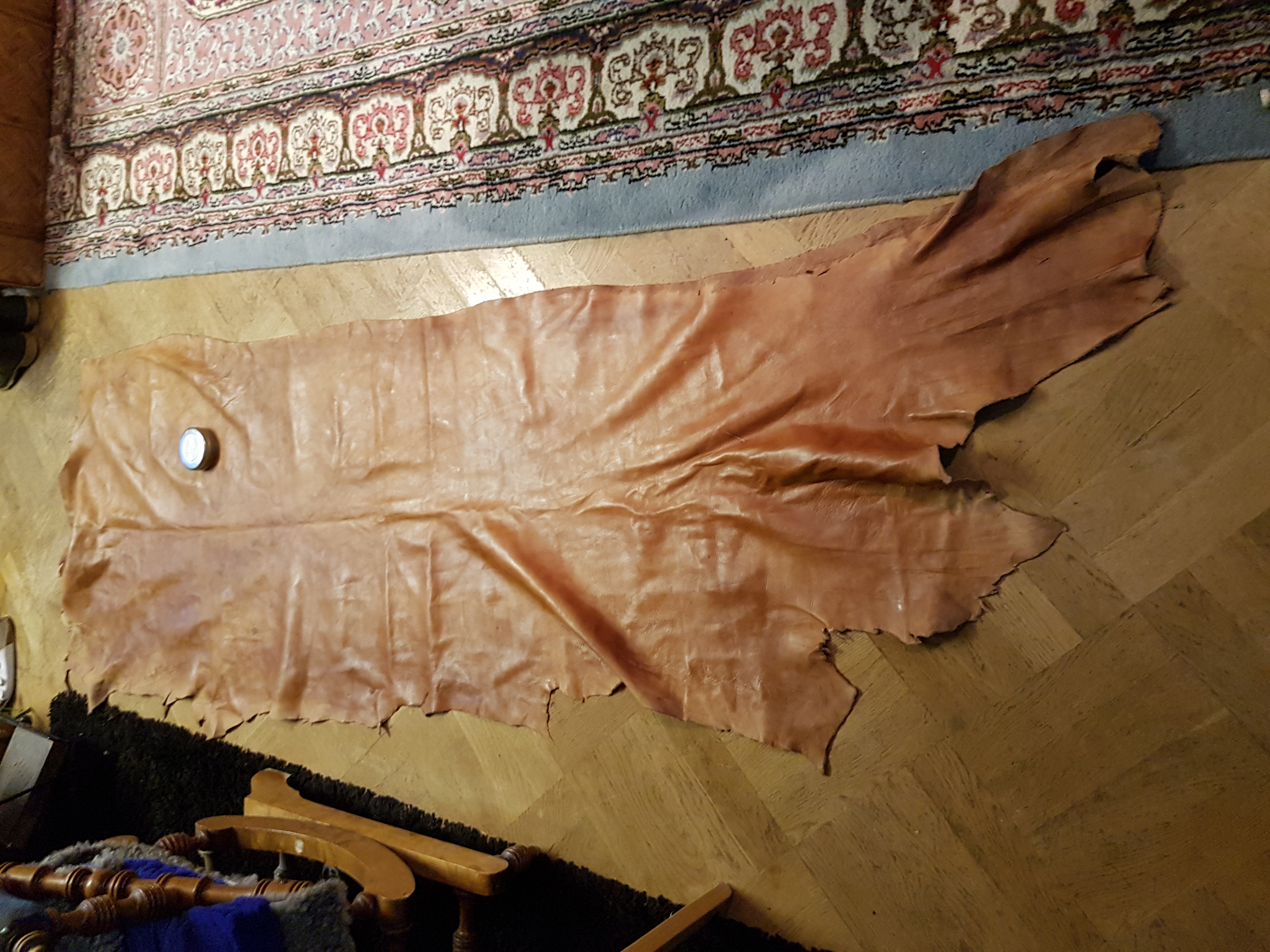
Personally, I used the skin from an elk. Those are normally full of holes from bug bites, but this one was nice and good to work with.
Unfortunately, I didn't take any photos of the cut-out leader parts. They should however be more curved on the upper part than the lower part. If you got material to spare the hinges could be cut out in the same piece as the sides, but otherwise you'll have to use separate parts for hinges and sides.
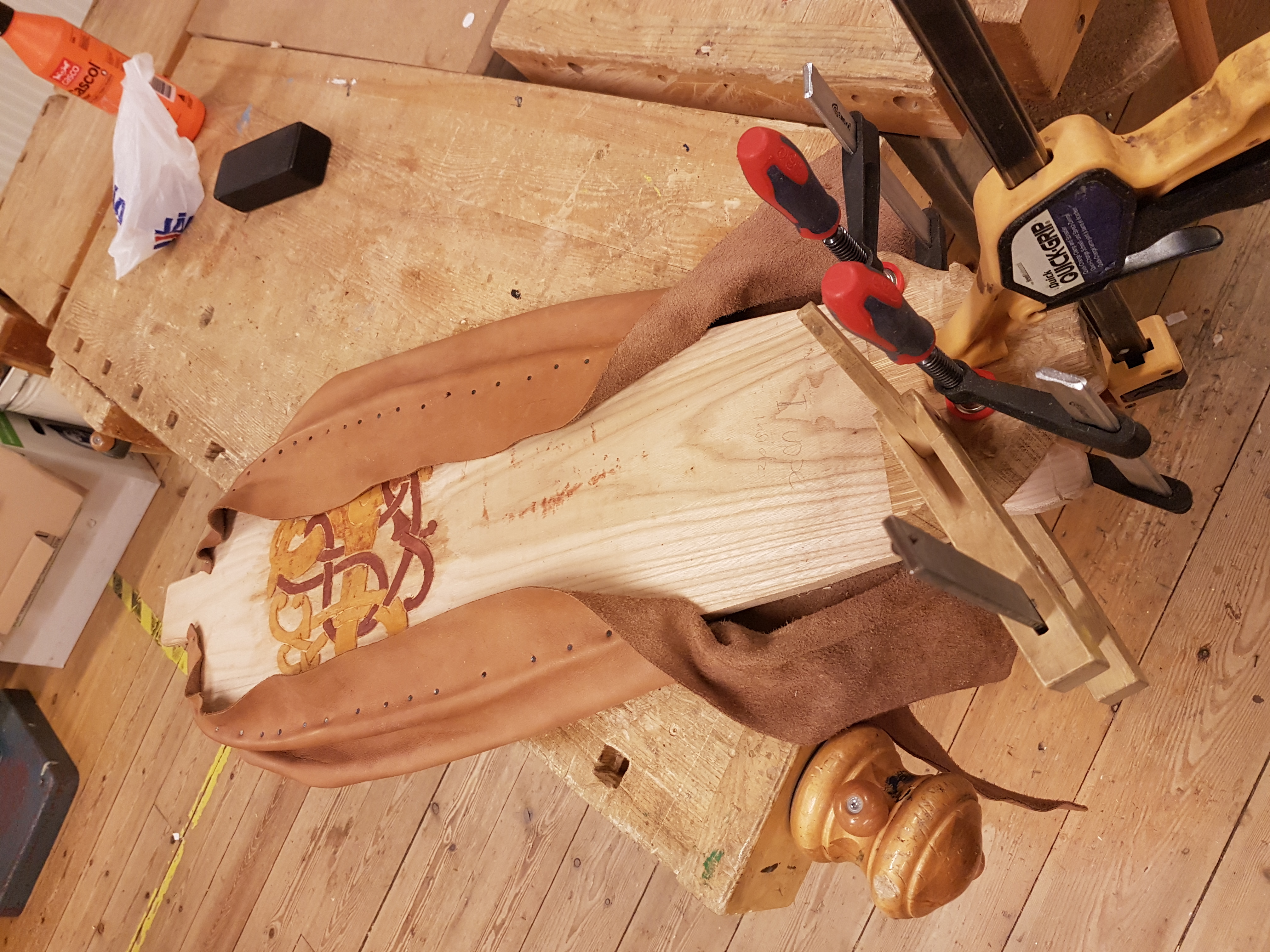
To fasten the leather parts I had to resort using blocks of wood as a distance between bottom and top to be able to hammer the nails down.
I don't know if it's true, but I've somewhere heard that ancient bellow leathers are coated with honey on the inside to make them tight. I assume that would draw ants, but the disinfecting properties of honey might preserve the leather in a good way.
Hinges
The hinges are just another piece of leather to reinforce the first layer.
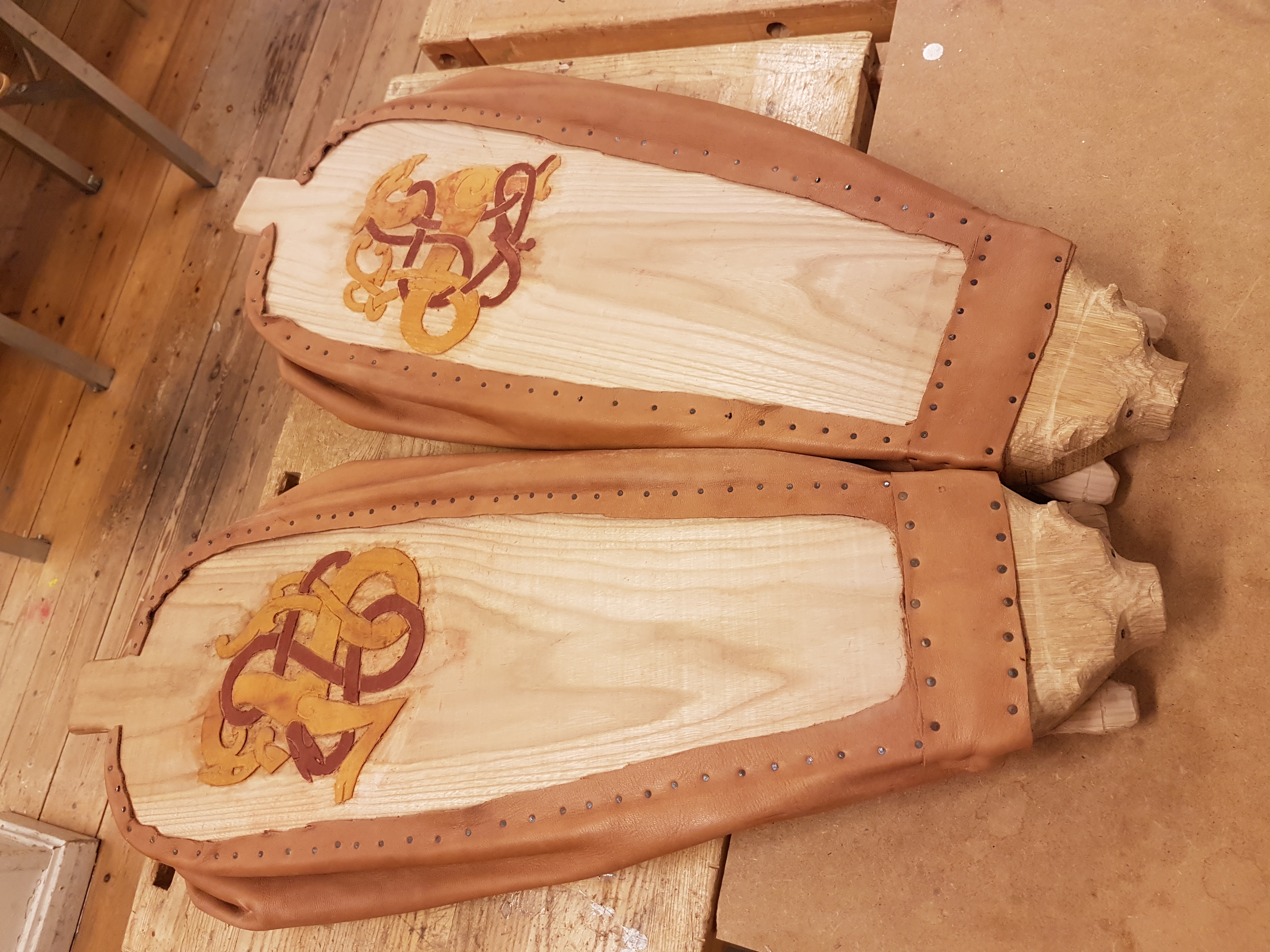
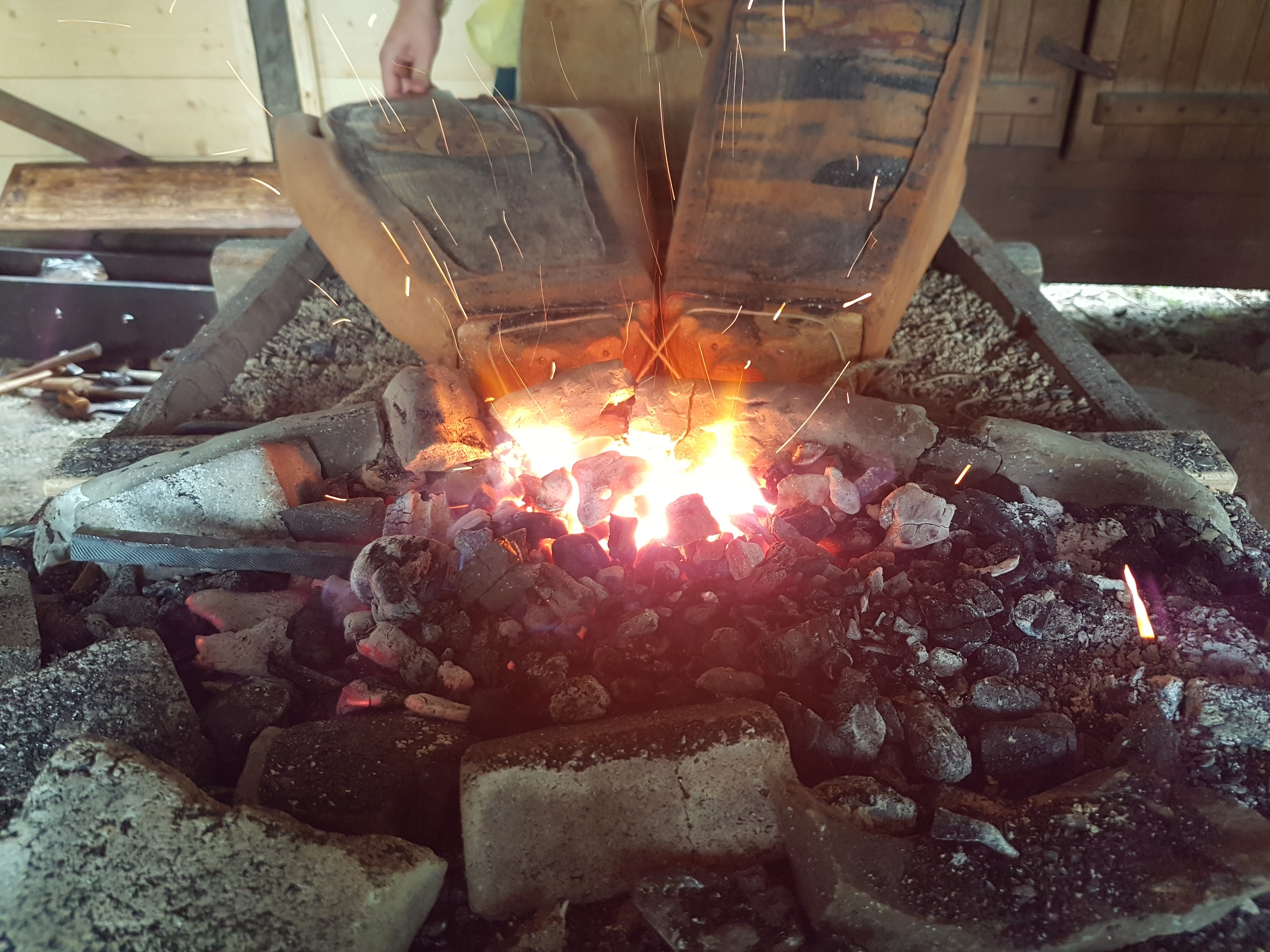
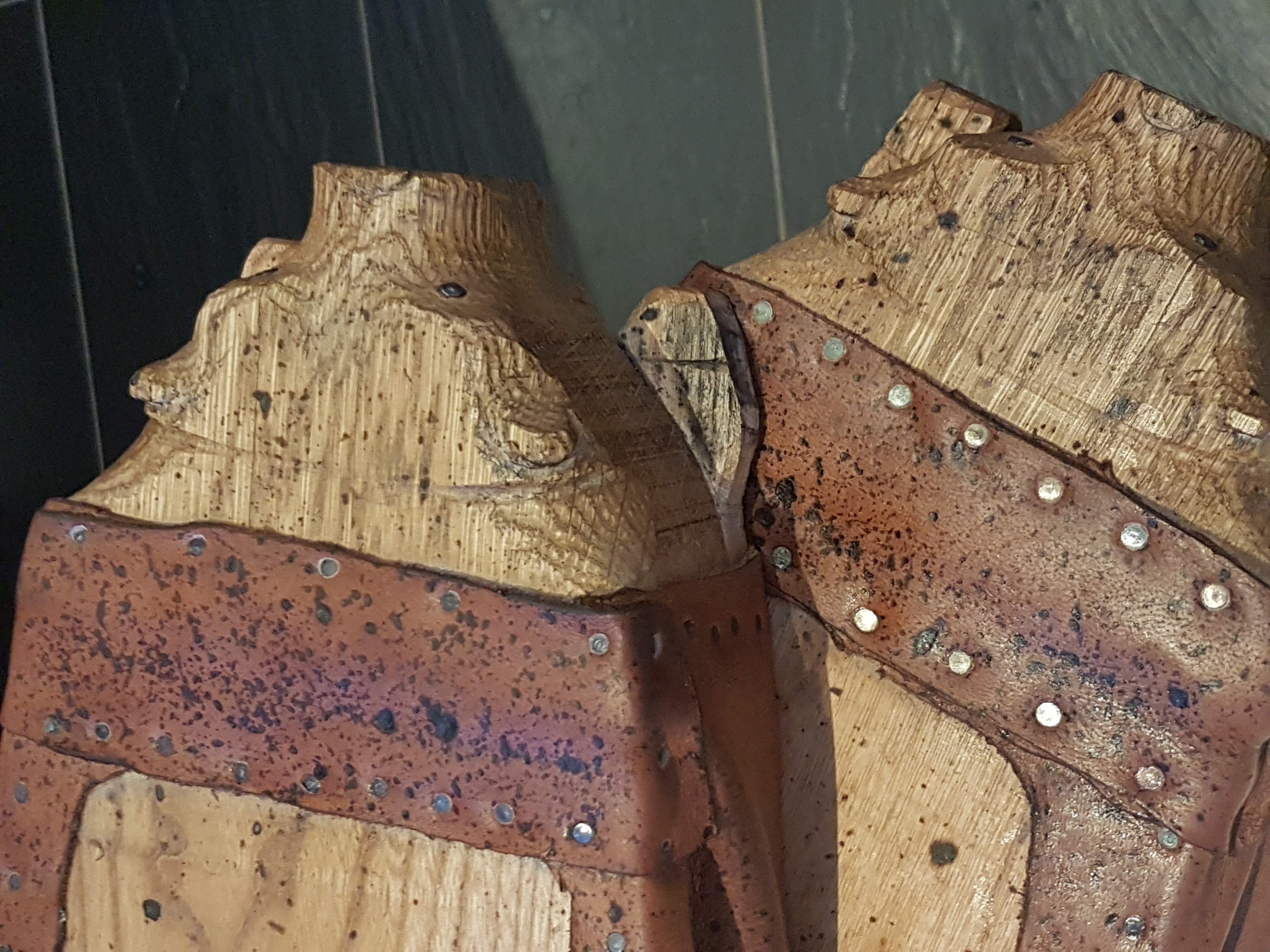