Small knife
Since my kids were small, I've withheld a strong rule that the kids had to be three years old to start using knives for woodwork. When they became ten years old, they got a knife of their own, or at least that was my idea.
When my oldest daughter turned ten, she of course wanted a knife of her own, and we went around markets trying to find the perfect knife. She found several she fancied, but I was not satisfied with them. Eventually I found a knife blade I really liked and bought that to make her a knife myself. Unfortunately, the blade was lost before I got the chance to create the knife and she didn't get any ten year old knife. :/
Almost 15 years later the blade surfaced in the bottom of a chest. The same daughter now was about to celebrate her 25:th birthday, I got going producing the knife once promised.
During the work I took a few pictures, that can be seen below.
The knife is made to be able to wear it in the belt, but also as part of a viking women's pearl band.
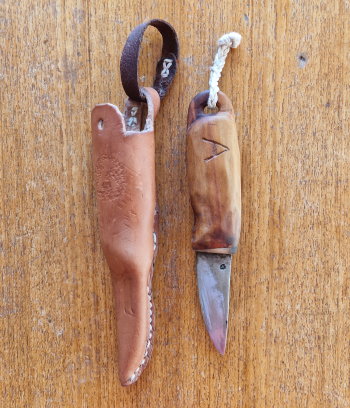
For inspiration I my memory of a knife that Anne Grootmak showed me this summer. A small knife she wore with her viking clothing, by the bosom.
A knife that small need to have a handle that is really thought-through.
Blade
The blade is short since it was bought for a ten-year-old. A short blade is good since you get great cutting force without having to apply a lot of force yourself. The shape is triangular as were the viking age and medieval knifes. Short blades are surprisingly useful, and often to be preferred over long blades.
Handle
To create the handle, I used a piece of wood I found laying around. Probably birch.
For a well-fitting handle I had a tilting slope closest to the blade - for a good grip with the index finger. The pinkie-finger rests on the shelf in the back end of the knife.
The sloping style of the handle closest to the blade was a mistake since the blade wasn't cut that way. Hence, I had to put in a wedge to even things out and close the gap. I choosed a whiter wood for this for decorative effect. This wedge was glued in place.
I carved an A into the handle as well. A for Alva, the name of the recieving daughter.
I knew the handle would be short, so I wanted it to feel good in the hand, but also to be as short as possible. To still be able to pull it from the sheath I made a hole in the top of the handle to attach something softer to pull the knife from the sheath. Not yet having any idea of what that would be, but an idea that it shouldn't be a loop since that could get caught up in something - pulling the knife from the sheath unintentionally.
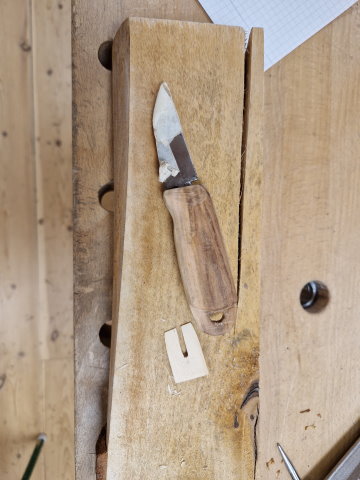
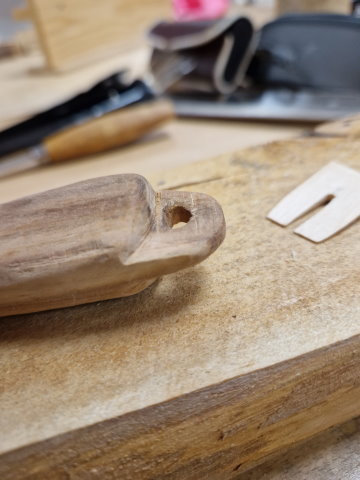
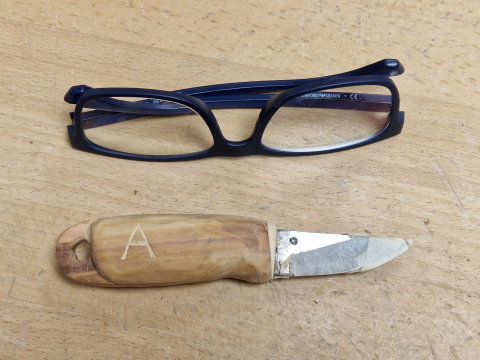
Since the hand size of my daughter is smaller than my own hand, I had a few people with smaller hands try the knife. They said it was feeling good in the hand, so I went on with the sheath.
When the woodwork was done, I smeared it in leather wax for protection. Yes, leather wax can be used for wood too.
Fastening the blade to the handle
When fastening the blade to the handle I usually create a false tongue with about the same dimensions as the actual protruding part of the blade, then heating it up to almost red glowing and pushing it into the wood. Normally it's possible to push it about a centimetre in per heating, and when I've burnt long enough into the handle, I can hammer the blade in place. This time I opted for another way of fastening the blade since I was too lazy to fire up the forge.
I drilled a hole into the handle, for the tongue of the blade.
To make it fit better I used a small file to widen the hole and then filed a bit on the tongue of the blade to make it sharp like a chisel, then I hammered the blade in place into the handle. I could have used glue of course, but since the hole had a bit of charcoal left from a dull drill it stuck very well without it.
Although the blade had become dull over the years, I put tape over the edge of the blade for protection while working with it.
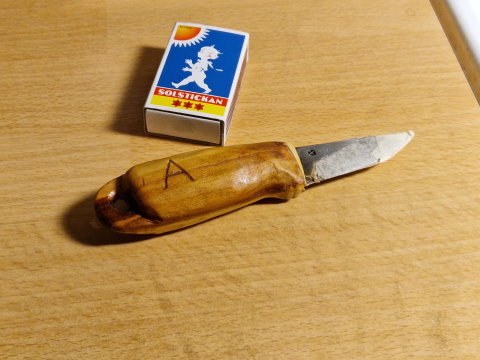
Sheath
For the sheath I opted for one in thicker leather, but without wooden frame. A wooden frame is good for long and thin blades, to protect them. This short knife would not benefit from this, it would only make the sheath heavier.
I wanted the seam of the sheath to be on the back side of it rather than on the edge side of the blade - and a tight grip of the knife in the sheath so it won't fall out, so I had to form the sheath before sewing it together.
Forming the sheath
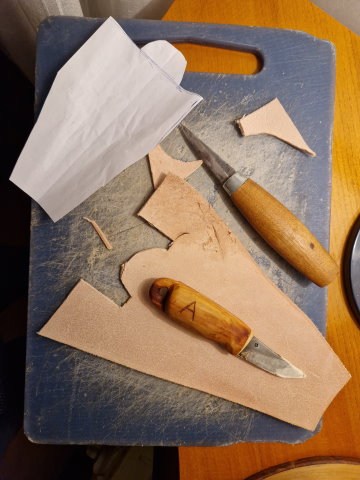
Initially I had an idea to use strips at the top of the sheath to sew down as belt loops. This was a bad idea mainly because the leather was torn by one of the strips. Instead, I eventually used other fastening methods.
I was in a bit of a hurry to produce the knife and sheath since the birthday was coming up fast. If I'd taken more time, I'd make sure the dents from clamps would be softened by using something between the leather and them. That was my initial idea, but I opted out of it from time pressure. I had even cut pieces of discarded thick leather to use for this.
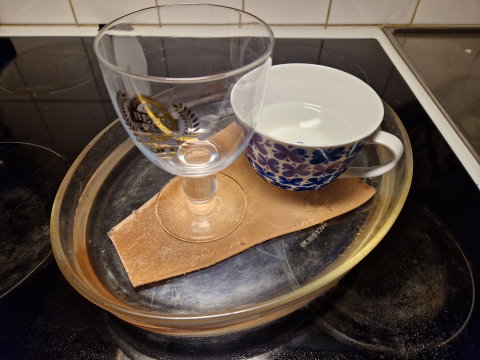
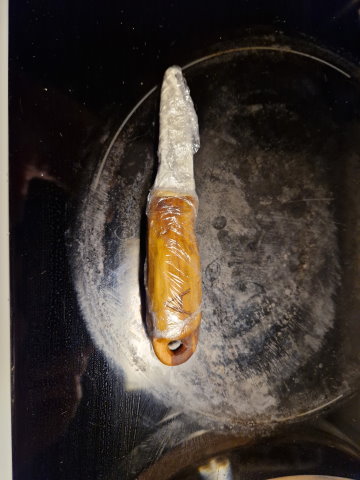
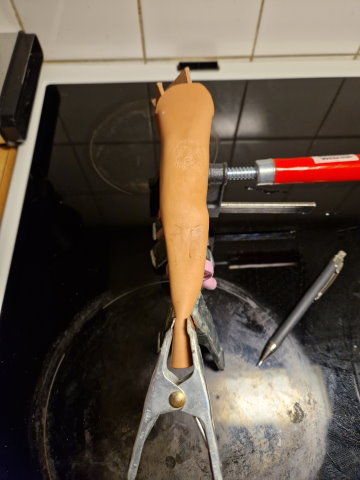
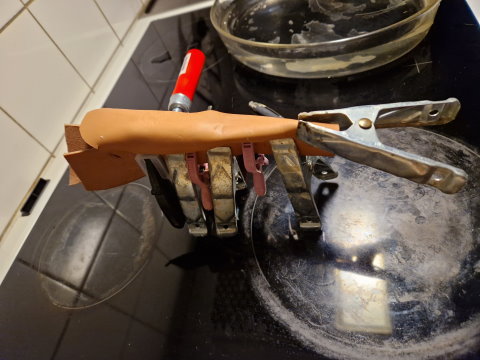
When the leather was wet, I also tried to decorate it a bit by pushing the letter A into it (A for Alva, the name of the daughter receiving the knife). Looking at the result I realize I should have been wearing my glasses.
The sheath was left to dry overnight.
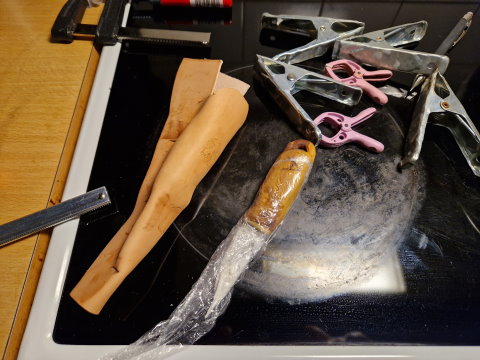
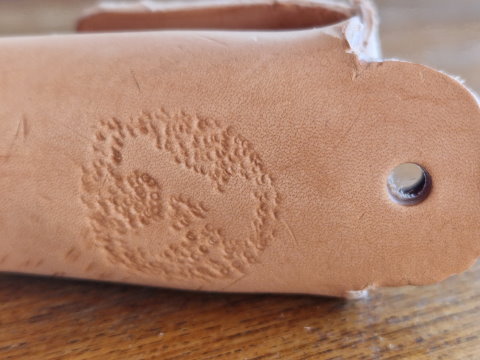
Sewing the sheath details
The sheath was sewn together before cutting away excess material. I had to re-think and re-design the sheath fastening a few times before I was pleased with the result.
The seam used was saddle-making seam with two dull needles and pre-made holes by the manual use of an awl.
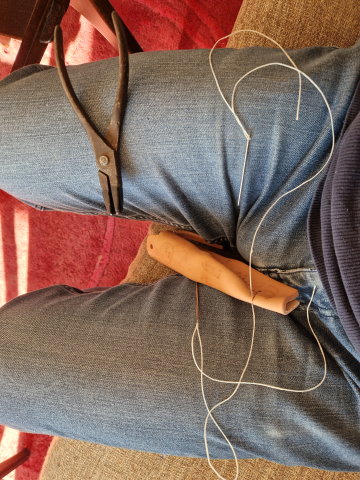
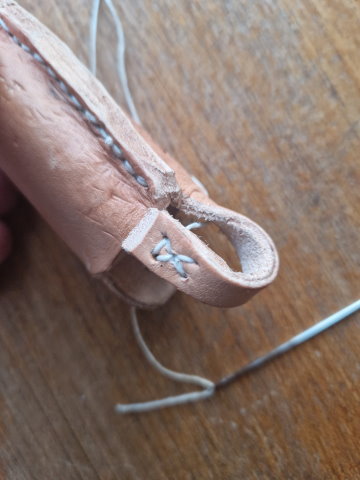
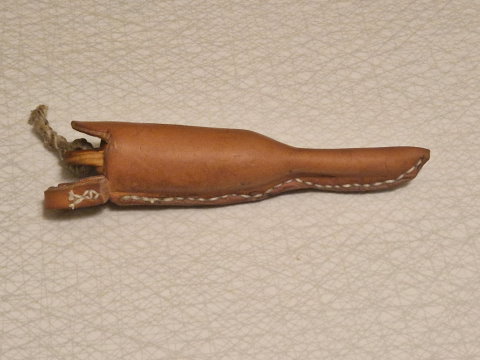
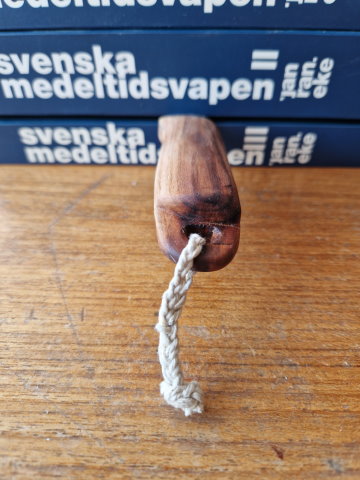
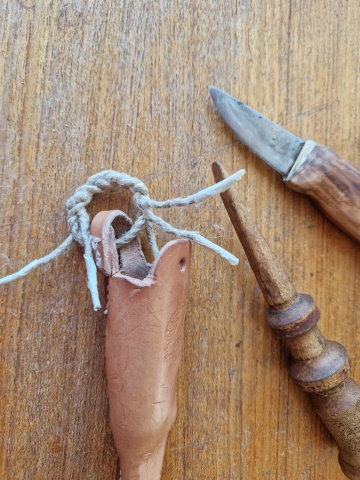
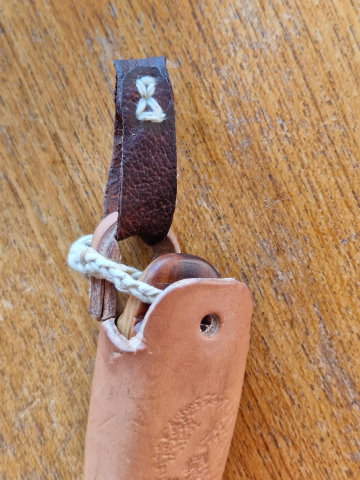
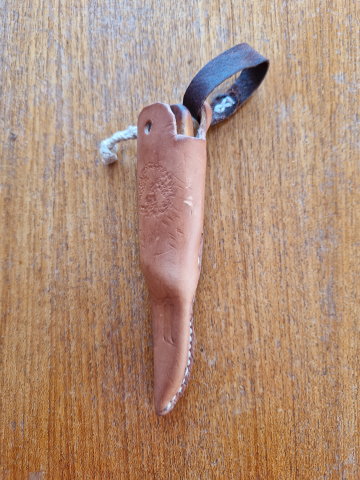
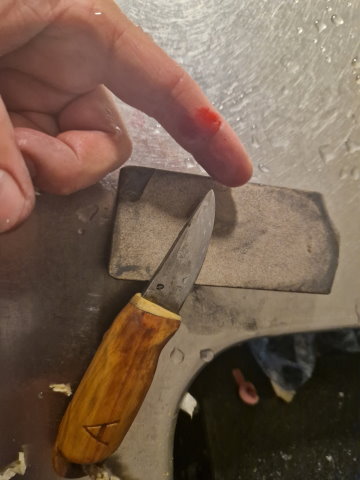
Lessons learned
- Use glasses when decorating leather
- The front top leather part with the hole on the sheath was un-necessary and could be cut off
- It's not a problem trying out different solutions until you're satisfied
- If you've got time - use linseed oil for wood protection
- Don't stop decorating because you are afraid you'll ruin the piece. The eye is drawn to the best-looking parts, ignoring the worst.
- Avoid being overly tired when sharpening knives
- Mixing different types of leather could still be beautiful